Custom Automation vs. Off-the-Shelf Solutions: Which Is Better?
March 5th, 2025
4 min read
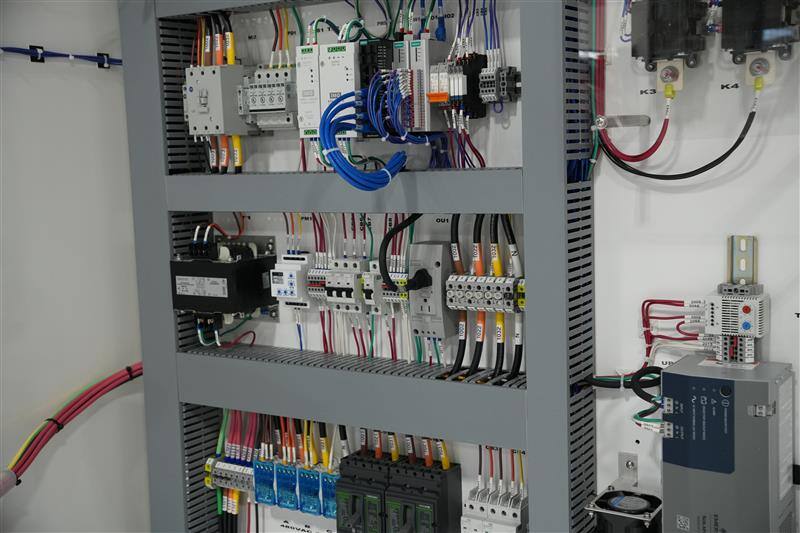
When you start planning a new automation project, the first question often isn’t how you’ll automate, but what kind of system you’ll use to get there. You have options, and that can make the process overwhelming. Should you buy a pre-engineered, off-the-shelf solution that’s ready to install? Or do you invest in a custom system built specifically for your process?
It’s not just a budget question–it’s a decision that could affect your production, your operators, and your long-term flexibility for years to come. At ASG, we’ve helped countless facilities walk through this choice, and here’s what we know: there’s no one right answer, but there is a right answer for you.
Custom vs. Off-the-Shelf: What Are You Really Buying?
Custom automation is designed for your process, your equipment, and your facility’s physical layout. It starts with your goals and works backward to design a solution that fits, rather than forcing your process to adapt to what’s already available. That’s why custom automation tends to work best in highly specialized processes, older facilities with legacy equipment, or lines that need to handle frequent product changes.
Off-the-shelf systems are ready-made solutions designed to handle the kinds of automation challenges that most facilities face — things like simple conveying, filling, labeling, or palletizing. These systems are quick to deploy and often come at a lower upfront cost, but they aren’t built for your specific process. That means they might require modifications, workarounds, or compromises to fit into your production environment.
The Cost Factor: What Does “Cheaper” Really Mean?
If you’re only looking at purchase price, off-the-shelf almost always wins. It’s less expensive upfront, and for some facilities, that’s the deciding factor. But if you look beyond the initial investment, the story changes.
With a custom system, you’re paying for engineering and design up front — but that investment pays off in efficiency, reliability, and reduced maintenance headaches. Custom automation fits your process from day one, so your operators aren’t constantly compensating for mismatches, and your maintenance team isn’t chasing compatibility issues between new and existing equipment.
Off-the-shelf solutions, on the other hand, come with lower upfront costs — but they often bring hidden costs after installation. Adapting the system to fit your existing equipment can mean extra hardware, programming changes, and even physical rework on your line. Over time, those “quick fixes” can turn into expensive long-term problems, especially if your process changes and the system isn’t flexible enough to evolve with you.
With a custom system, you’re paying for engineering and design up front — a capital expenditure (CAPEX) — but that investment pays off in efficiency, reliability, and reduced maintenance headaches over time. Off-the-shelf systems, on the other hand, come with lower capex but often bring higher operational expenditures (OPEX) after installation, as you adapt and maintain the system to fit your process.
How Much Time Do You Have?
Another big concern for many facilities is speed. If you’re replacing failed equipment or responding to a sudden production demand, off-the-shelf solutions are appealing because they can be delivered and installed fast. That speed can be a lifesaver in an emergency.
But fast doesn’t always mean smart. If your process is complex or if you have specific quality standards to meet, a quick off-the-shelf fix can introduce new problems — ones that might slow you down in the long run. Custom automation takes longer to design and build, but that time investment gives you a system that works right the first time, with fewer surprises down the road.
What if Your Process Changes?
Your production needs today might not look the same in five years — or even next year. That’s something every manufacturer worries about when making a big equipment investment. What happens if you need to run a new product, increase capacity, or meet new compliance requirements?
This is where custom automation shines. When you work with a design-build partner like ASG, the system is built with flexibility in mind. Need to add another product variation? Swap in a new piece of equipment? Adjust your inspection process? Custom systems can be modified more easily because they were designed to flex from the beginning.
Off-the-shelf systems, by contrast, are what they are. If your needs change, you may find yourself limited by what the system can do — or facing expensive rework to force-fit new requirements into a rigid design.
Who Supports You When Something Breaks?
Every piece of automation equipment eventually needs maintenance, and when that time comes, the kind of system you choose can make a big difference.
With custom automation, you have a direct line to the team who built it. They know your system inside and out because they designed it for you. That means faster troubleshooting and more effective repairs.
Off-the-shelf systems often come with broader support networks, which can be convenient — but generic support teams don’t always understand the specific modifications you made to fit the system into your process. That can turn a simple fix into a drawn-out troubleshooting exercise.
The Questions You Should Ask Yourself
If you’re still torn between custom and off-the-shelf, step back and think about your process, your operators, and your long-term goals. Here are the questions you should be asking:
- Is my process standard, or does it have unique challenges?
- How important is flexibility if our products or requirements change?
- How fast do I need this system installed?
- What’s more important–the lowest upfront cost or the lowest total cost over time?
- Do I have existing equipment that the new system needs to work with?
If your process is straightforward, and you need something fast at the lowest possible cost, off-the-shelf may be the right call. But if your process is unique, your existing equipment has quirks, or you’re thinking long-term, custom automation is almost always the smarter investment.
The Truth About “One-Size-Fits-All”
It’s easy to fall into the trap of thinking off-the-shelf systems are simpler and more reliable because they’re standardized — but the truth is, no automation system is truly plug-and-play. Every facility has its own physical layout, process variations, operator preferences, and production goals. Even off-the-shelf systems often require adjustments and workarounds to fit real-world conditions. The question isn’t whether you’ll need customization — it’s how much, and whether it’s better to do that work upfront or figure it out as you go.
Final Thoughts: Making the Smart Call for Your Facility
At the end of the day, this decision isn’t about technology — it’s about what’s right for your business. The system you choose has to work for your operators, your maintenance team, your production goals, and your budget. It has to solve the problems you have today without creating new ones tomorrow.
At ASG, we’re here to help you make that decision with clear, honest advice. Sometimes, that means designing a fully custom solution. Other times, it means helping you select the right off-the-shelf system — and making sure it’s adapted correctly so you get the performance you need. Either way, the goal is the same: automation that works for you, not the other way around.
If you’re weighing your options, let’s talk. We’ll walk through your process, your goals, and your challenges — and we’ll help you map out the smartest path forward. Contact us today to get started.
Topics: