7 Things You Need to Consider When Working With a Panel Builder
March 10th, 2025
5 min read
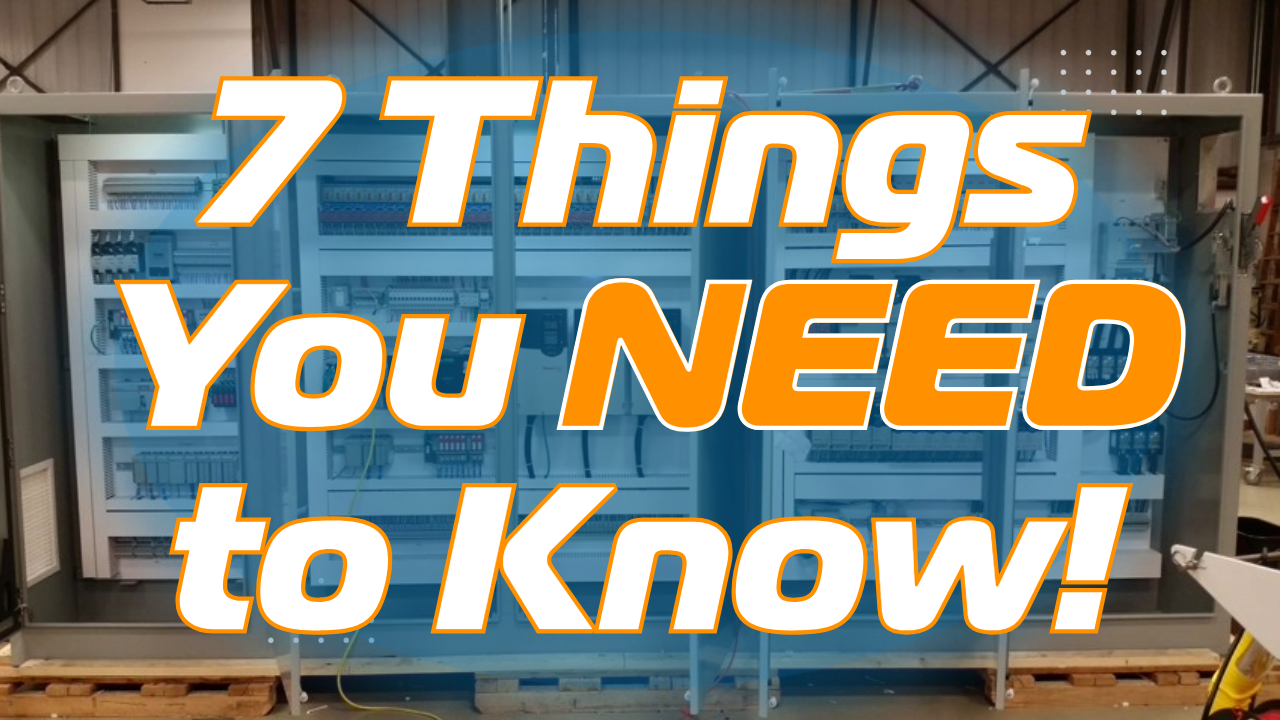
When it comes to manufacturing for industrial automation, it is essential to work with an experienced panel builder who can deliver what you need: a control panel made to your specifications that fits your needs.
A seamless partnership with your panel builder can differentiate between a smooth project with a result that meets your needs and a project stricken with costly delays. With so many variables to manage—from certification requirements to environmental challenges—manufacturers need a clear roadmap to ensure success.
The ASG team has over two decades of experience building electrical control panels and has learned firsthand what you need to know. In this article, we’ll explore seven critical considerations you should make when working with a panel builder.
UL Certifications
The standards developed by Underwriters Laboratories are widely recognized as best practices for manufacturing, and testing the safety, security, and sustainability of products and systems. These include fire and flame resistance, functionality, potential electrical hazards, and much more.
To ensure safe use for personnel and compliance with regulations, as well as compliance with the National Electric Code, many projects require products to meet UL standards. Ignoring these standards could result in project setbacks if it fails to pass the necessary inspections, the outright rejection of your project, or safety hazards for your project and anyone who interacts with it.
When planning your project, make sure to check and see if you’re required to meet any standards. Tell your panel builder about these requirements upfront so you can make sure they can meet them.
Voltage Range
Voltage range refers to the amount of power your system will be working with. There are generally three ranges:
- High Voltage (HV) - 115,000 to 1,100,000 VAC
- Medium Voltage (MV) - 2,400 to 69,000 VAC
- Low Voltage (LV) - 240 to 600 VAC
Panel builders often have specific capabilities when it comes to the voltage ranges they build for. Depending on the voltage level of your project, you’ll need to confirm that your panel builder is able to meet your needs.
Addressing this early in the build process ensures compatibility and saves you from unnecessary delays later down the line. Ask your panel builder if they have the supply chain to acquire the parts you need and the facility to meet your projects’ demands.
Size Constraints
Another crucial consideration to make is size–both the size of your project and the space your panel builder has to make it.
It’s common for manufacturers to focus on functionality and lose sight of how the design's physical footprint fits within the panel's physical dimensions. If the crucial components of your panel don’t fit together, you run into the obvious issue of not having a working panel! Planning ahead during the design phase is an easy way to prevent this.
Similarly, your design might work just the way you want it to, but it’s also important to consider where your panel builder is doing their work. Make sure they can accommodate not just the final size of your project, but the space necessary to build it.
Mounting Options
When it comes to mounting your panel, there are generally four options to consider:
- Pad-Mounted: installed on a concrete or other stable foundation at ground level, and typically used in outdoor environments where accessibility and durability are key, such as utility distribution, industrial facilities, or outdoor commercial applications.
- Wall-Mounted: mounted directly to a wall or vertical structure, these panels are ideal for indoor applications and some protected outdoor environments. They are common in residential, commercial, and industrial settings for controlling electrical circuits, motor control centers, or breaker panels.
- Skid-Mounted: pre-installed on a skid, a steel or aluminum frame designed for portability and easy installation. They’re ideal for temporary installations, remote or rugged locations, and environments requiring high mobility, such as oil and gas fields, mining operations, or construction sites.
- Free-Standing: self-supporting and typically mounted on legs or a robust base, making them ideal for floor installations in various environments, such as industrial, commercial, and utility sectors for managing large or complex electrical systems.
There are advantages and disadvantages to each mounting method, but what’s important to consider is that each method impacts the design and materials needed.
You should discuss the mounting options that are right for you with your panel builder before the build process starts to ensure a smooth manufacturing process and seamless integration when the panel makes it to the field.
Timelines and Procurement Strategy
Panel building is not an instant process; your builder will need time to collect materials, manufacture the panel, and do any necessary testing. This is why it is critical to communicate your project deadlines upfront and set clear expectations.
Also, make sure to discuss your procurement strategy, which is the process by which your project’s parts will be retrieved. Does the responsibility to provide parts fall to you? Will the panel builder handle sourcing? This can prevent unnecessary expenditures, repeated purchases, and of course, project delays.
Environmental Factors
Closely related to the mounting options mentioned above, the location of your panel will have a significant effect on the manufacturing process.
Panels located in volatile environments will have different material needs than those located in controlled indoor environments, and you and your panel builder need to consider this factor when sourcing parts with the right durability and reliability.
One easy way to know if a material is right for the environment where your panel is located is the NEMA (National Electrical Manufacturer Association) rating, a rating system that specifies the types of environments an electrical enclosure can handle and indicates how well the enclosure can withstand specific environmental conditions. Some common NEMA ratings include:
- NEMA 1: ideal for general-purpose indoor installations where minimal environmental protection is sufficient, with protection against accidental contact with live parts and limited amounts of falling dirt
- NEMA 3: designed for outdoor use, providing protection against weather conditions like rain, sleet, and snow
- NEMA 4: designed for indoor and outdoor use, with protection against everything NEMA 3 covers as well as water spray and corrosion
The NEMA rating of a given part will be specified by the manufacturer. Make sure you know what environmental factors your panel enclosure will be facing to make sure you get the protection you need.
System Integration
System integration is the glue that connects your panel to the rest of your automation ecosystem. Whether it’s a production line, a building’s electrical system, or a broader industrial network, clear integration planning ensures compatibility and smooth operations.
Consider how your new panel will interface with the rest of your system. Will wires enter from the top, bottom, or sides? What types of connections do you need for it to interact correctly with your other devices?
Establishing communication standards is critical in industrial environments where multiple devices must share data. For example, Fieldbus or Ethernet/IP protocols are often used to maintain consistency and reliability in data exchange.
The environmental conditions mentioned above also come into play here. Make sure that the connections you need are rated correctly to withstand anything thrown at them. Provide all of this essential information to your panel builder to ensure that they can meet your needs completely.
Starting Your Project
These seven considerations are some of the most important things to consider when you start working with your panel builder. But there’s another piece of the puzzle that has been hinted at throughout this article: the importance of good communication.
Simply put, the only way to truly ensure that you stay on time, within budget, and have an overall efficient experience is to talk openly and honestly with your panel builder. This way, they know what you need from them and you know what they need from you at any point in the process, and if changes or amendments need to be made, they can be done in as little time as possible.
Setting up a standardized way of talking to your panel builder regularly may be helpful. Keeping these lines of communication open will ensure a smooth process for everyone involved, whether you’re having weekly video calls, employing a website with collaborative features, or just committing to send updates via email.
At ASG, we aim to provide you with the guidance you need for a successful project. Contact us today with any questions you might have about the panel-building process, or if you’re looking to start a project with us.
Topics: