The Insider’s Guide to UL Certifications: Elevate Your Manufacturing Facility
August 8th, 2024
4 min read
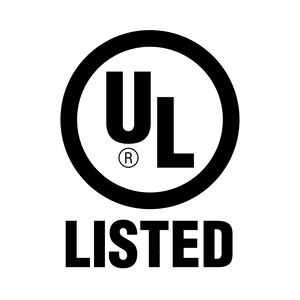
Nearly all production lines require some sort of ‘code’ to be met when products are created. Whether it is an embellishment that states, “Made in America” or a standard that must be met to make it a safe product, a code is always prevalent.
Products in manufacturing facilities need to be up to code because they run factories that require high power and voltage. If something goes wrong or malfunctions, it can cause an enormous mishap, like a fire or explosion, that can leave your facility and employees in trouble.
Some certifications can be put in place to ensure that products created in the facility meet local and federal safety and environmental regulations.
At ASG, we obtain numerous UL standard certifications that give us the ability to produce safe and sustainable products that meet those local and environmental regulations. But these certificates are not necessarily required by law – so what makes them so important?
We are going to explore the importance of UL certifications and how choosing to purchase products that meet these regulations will positively impact your facility.
What is a UL Certification and What Are Common Types in Manufacturing?
UL standards are certificates granted by Underwriters Laboratories (UL) after products, systems, or services are evaluated to ensure they meet specific safety, performance, and sustainability standards.
UL was established in 1894 as the Underwriters’ Electrical Bureau and during the 20th century moved over to the name Underwriters Laboratories (UL). In 1903, UL’s first standard for safety was published and was implemented in public spaces like warehouses, schools, and hospitals.
Fast forward to 2024, there are now over 1,000 UL standards that manufacturing facilities can obtain to ensure the products coming out of that facility are safe and sustainable. You’ve probably seen their logo on just about everything, from your refrigerator to your cell phone charger.
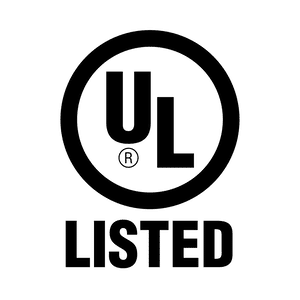
Source: Seal & Design
UL certifications can significantly enhance product credibility, marketability, and regulatory compliance. They demonstrate a commitment to safety and quality, which is crucial for building trust.
For you, a UL certification can provide some assurance that the products you are purchasing have been independently evaluated for safety and reliability. This is vital in industries where safety is paramount – like manufacturing.
In the manufacturing and renewable energy sectors, several UL certifications tower above the others, like UL508A, UL98B, and UL1741. Though these are not the only ULs available, they play a major role in ensuring the electrical equipment in your facility is reliable.
- UL508A is a standard that covers industrial control panels, which are always a major part of manufacturing facilities. These standards dictate design and installation requirements for various components found in manufacturing facilities, like enclosures, drives, switches, circuit protection, transformers, and more. This standard ultimately ensures that the elements are safely and effectively integrated.
- UL98B is a standard that covers enclosed and dead-front switches for photovoltaic systems, ultimately handling voltages up to 1500vdc. These standards dictate the design and testing requirements for switches to be used.
- UL1741 is important for products like inverters, converters, controllers, and interconnection system equipment that is used with distributed energy resources.
UL certifications and standards directly impact the safety and quality of products manufactured. They ensure that every stage of the product lifecycle – from designing to manufacturing to testing – maintains a high level of quality.
When your company invests in certified products, you are investing in manufacturers who do things the right way. Earning these certifications is an intensive process. There are five main steps:
- Identifying Customer Needs
- Determining Needed UL Certifications
- Design and Documentation of Product
- Testing and Feedback from UL
- Final Approval from UL
Investing in products that are UL-certified increases your chances of operating a safe and sustainable facility with high-quality, high-functioning products. But what makes these products stand out for manufacturing facilities?
The Importance of UL-Certified Products in Your Manufacturing Facility
Now you know what UL certifications are and have a general idea of why they are implemented. However, understanding the importance of obtaining them is going to give you a better idea of why this is such a big deal in the facility.
When it comes to creating your facility, you need to be thinking of three main aspects: safety, quality, and reliability. UL certifications stand as a hallmark for all three of these and provide significant benefits for both the manufacturer and you.
Ensuring Safety
The primary advantage of UL-certified products is the assurance of safety in your facility. By implementing these products, you are proactively safeguarding against any potential hazards like electrical shocks, fires, or mechanical failures.
Not only does this protect your employees, but it also minimizes the risk of costly accidents and liability issues.
Enhancing Product Quality
Another advantage is the product quality. The certification process involves comprehensive testing and evaluation to ensure that every product meets or exceeds performance standards. By integrating UL-certified components into your manufacturing facility, you are investing in products that are designed to the highest quality.
Having your facility committed to quality translates to more consistent production processes, fewer equipment failures, and reduced downtime – all of which contribute to a successful production line.
Boosting Marketability and Reliability
Lastly, when your company purchases a manufacturing product that is UL-certified, it is a mark of credibility and trust. When your company has these products, your customers will be more apt to fully trust what you are producing because they know your products have been produced with full credibility, increasing the reliability they have in you.
When your machines have that UL mark, it can be a deciding factor in purchasing decisions. Not only is your company ensuring performance standards, but also enhancing the marketability of your products. Future customers and current ones are more likely to trust and invest in your products that have been verified for their safety and reliability.
You’re Informed: Purchase UL-Certified Products for Your Facility
Now that you have gained knowledge of UL certifications and why they are important to your manufacturing facility, we recommend doing your research before purchasing.
As with any product, it is important to weigh all your options before making that final decision. Choosing a manufacturer that can provide you with UL-rated products for your facility will ultimately enhance your credibility, safety, reliability, and marketability.
At ASG, we obtain UL508A, UL98B, and UL1741 – meaning, our products are rated to ensure safety in your facility. To get UL-certified takes time – it is a commitment to the process and in the long run, well worth it. It creates a different avenue for us to go down, bringing in a large customer base.
While we are well equipped and informed to manufacture any electrical equipment that falls under these standards, we understand we are not the only manufacturer to provide you with these products. But we are available to discuss these certifications with you.
If you are looking to purchase electrical equipment for your facility that can ensure safety, protect your facility, boost operation efficiency, and stand out in a competitive market, reach out to us today.
Topics: