Hazardous Rated Cable Assemblies: Built to Endure
June 23rd, 2025
3 min read
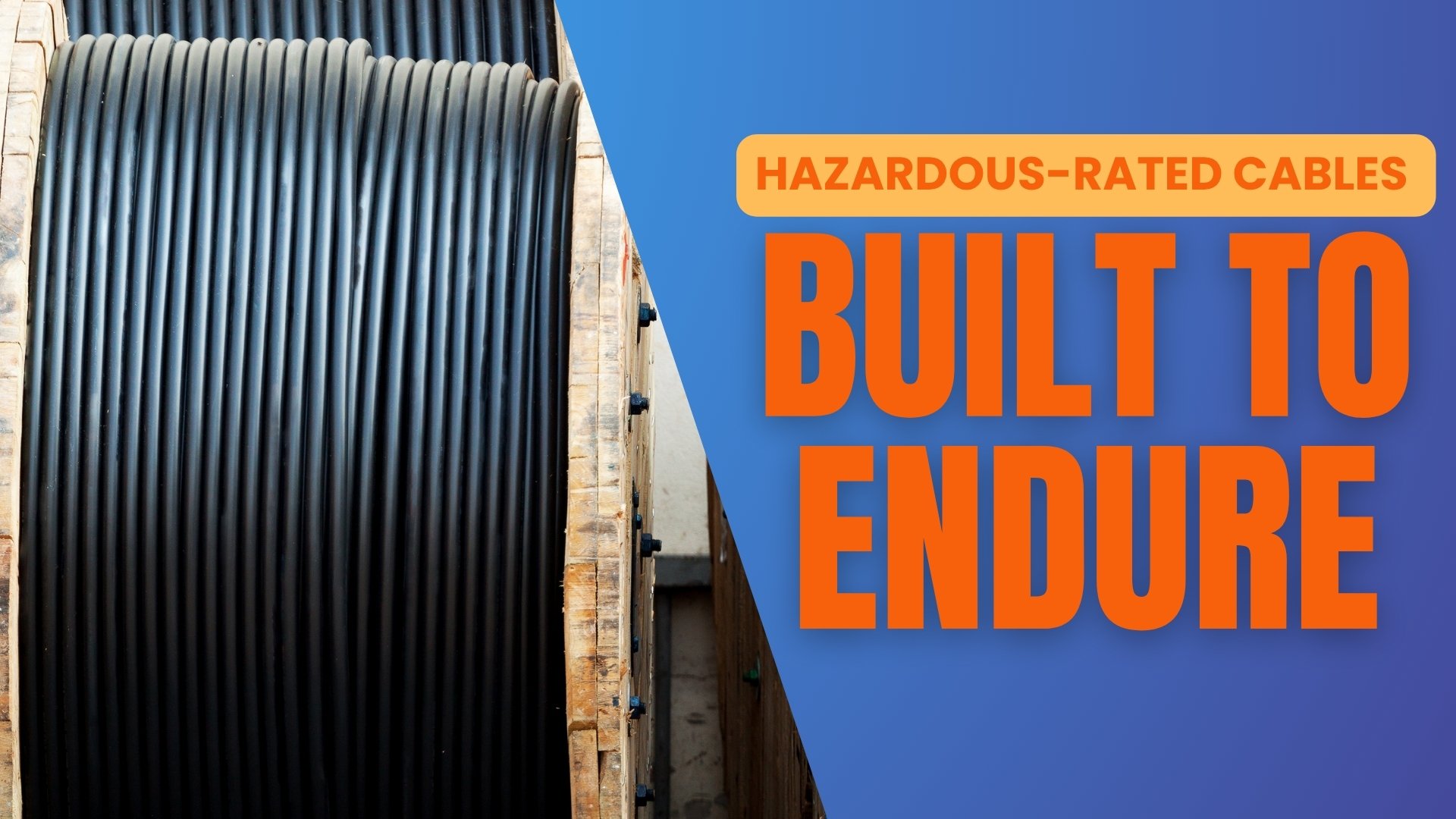
In the most demanding industrial environments, everything is tested. Equipment is exposed to punishing conditions: extreme heat, vibration, corrosive chemicals, moisture, and potentially explosive atmospheres. Any weak link can lead to costly downtime, compromised safety, or catastrophic failure.
At ASG, we design cable assemblies to withstand these extremes repeatedly and reliably. We serve industries where rugged performance isn’t optional. Our hazardous-rated cable assemblies are engineered for long-term use in conditions that break down standard solutions. With more than 25 years of experience, we've built a reputation for precision, consistency, and a clear understanding of what failure costs on a facility floor.
Engineering Rooted in Standards and Built for the Field
Every one of our technicians is certified to IPC/WHMA-A-620 standards, widely recognized as the benchmark for cable and wire harness quality. This standard provides the framework for excellence in manufacturing, but our work is driven by real-world applications that demand more than the minimum.
Each cable assembly undergoes high-voltage HIPOT testing, often up to 5,000 volts, and our systems are equipped to validate assemblies with as many as 200 conductors at once. This process confirms electrical reliability under pressure, especially important for installations in petrochemical, mining, and hazardous-rated production environments.
We also handle potting in-house, sealing conductor ends to block out moisture, dust, and arc faults. In critical installations, these sealed terminations contribute directly to operational safety and system longevity.
Built for the Unforgiving
Environments like oil rigs, chemical facilities, and mining operations don’t offer ideal conditions. Cabling is often exposed to abrasion, wide temperature swings, and heavy vibration. In these cases, system reliability is about more than performance on day one; it’s about consistency over years of wear.
We design every assembly with these demands in mind. Material selection is tailored to environmental stresses. Layouts and harness designs are built to fit without forcing bends, stressing connections, or creating clearance issues. We also consider how these assemblies will be installed, routed, and serviced, ensuring that technicians aren’t forced into compromises that could affect long-term reliability.
This process depends on close collaboration. We ask specific questions up front to understand how the assembly fits into the larger system. That dialogue gives us the insight we need to deliver solutions that hold up, regardless of where they’re deployed or how demanding the application may be.
A Systematic Approach to Quality
We integrate components from Amphenol Pyle National, a global leader in industrial connectors, particularly for hazardous locations. These are field-proven products that complement our assemblies in both form and function.
The use of high-performance components is important, but integration is where it counts. Our builds ensure continuity, physical fit, and environmental sealing from end to end. That means every connector, seal, and contact point is part of a coordinated system, not an afterthought.
This consistency supports more than operational uptime. It gives engineers and maintenance teams confidence in how systems will respond during commissioning, inspections, and emergencies. Every part of the build is deliberate, every component selected for a reason.
Custom Designs That Endure
Most of the assemblies we build are custom, but none of them are experimental. Each design is grounded in proven practices, tailored to unique specifications, and built to meet known challenges. Whether you’re supporting a legacy installation or rolling out new infrastructure, we take the time to understand what’s needed and why.
We provide documentation that supports inspection, troubleshooting, and future modification. Engineers can reference detailed specs, including conductor ratings, jacket materials, and termination types. This transparency makes ongoing system maintenance easier and ensures that what we deliver can be trusted over time.
As facilities modernize, the performance of cabling becomes even more important. Data transmission, signal integrity, and environmental resilience are now essential to digital infrastructure. Whether you’re integrating IIoT, predictive maintenance tools, or smart sensors, poor cabling can undermine system performance long before components fail. Our assemblies help preserve that reliability.
Precision You Can Depend On
Not all cable assemblies are created equal. In low-risk applications, a basic continuity check may be sufficient. But in environments with high stakes, where explosive gases, chemical exposure, or electrical hazards are present, the bar is much higher.
Our process is shaped by that reality. We trace every part. We test beyond standard voltages. We document not only what we used, but also how and why. Every step is built around repeatability and accountability. That’s what our customers rely on when lives, systems, and production schedules are at stake.
Whether you're installing into a Class I Division 1 enclosure or upgrading equipment in a 30-year-old production facility, the quality of your cable assembly can be the difference between routine success and unexpected failure. Our role is to remove that uncertainty and to keep it out of the equation.
Let’s Build It Right
Hazard-rated cable assemblies aren't plug-and-play. They require thoughtful planning, a deep understanding of the environment, and careful execution. Whether you’re troubleshooting an existing system or building something new, ASG is ready to support you with cable assemblies that deliver strength, clarity, and lasting performance.